The industrial world is constantly evolving, driven by the need for improved efficiency, lower costs, and better-quality outputs. One of the key drivers of this evolution is the implementation of advanced welding methods. These techniques not only streamline the production process. It plays a pivotal role in enhancing the overall performance of manufacturing systems. Significant advancements in welding technology have led to innovations that optimize operations across various industries, including automotive, aerospace, and construction. By understanding the impact of these modern welding techniques, businesses can adapt to the changing landscape of industrial production.
Understanding Advanced Welding Methods
Advanced welding methods encompass a range of techniques including laser welding, electron beam welding, and friction stir welding. Each of these methods presents unique advantages tailored to specific applications. Laser welding has gained traction for its precision and speed, making it particularly suitable for thin materials. This method utilizes the intense energy of a focused laser beam to create a strong bond, facilitating quick and efficient production cycles. Electron beam welding, on the other hand, offers the ability to weld at a much higher depth with minimal distortion, making it favorable for thick materials typically found in heavy machinery. This process operates in a vacuum, allowing for a clean and precise weld. Friction stir welding, which is a solid-state joining process, eliminates many challenges associated with traditional welding, particularly when it comes to metal fatigue and heat treatment. These advanced methods not only offer production advantages. They significantly reduce operational costs associated with traditional welding processes. By utilizing sophisticated equipment and techniques, industries have managed to lower energy consumption while increasing the strength and durability of the products they manufacture.
The Role of Automation in Welding
Automation has become an integral part of modern welding practices. Robotic welding systems provide consistency and precision that are difficult to achieve manually. These automated systems can operate continuously, allowing for increased production rates. They reduce the risk of human error, leading to fewer defects and wastage in manufacturing. Recent studies indicate that companies that implement automated welding processes experience a notable increase in production efficiency. As robots take over repetitive and time-consuming tasks, skilled workers can focus on higher-value activities that require critical thinking and problem-solving skills. This shift optimizes the workforce and enhances the overall quality of output, as the human element can be more effectively applied to tasks that require innovation or design adjustments.
Incorporating Specifications for Welding
Incorporating precise specifications for welding is crucial for achieving the desired results in any welding project. These specifications guide the selection of materials, welding techniques, and post-weld treatments necessary to meet quality assurance standards. By adhering to these guidelines, manufacturers can ensure that their products meet industry regulations and customer expectations. You should know that welding specifications play a significant role in maintaining safety standards within the workplace. With the rise of advanced welding techniques, engineers and technicians need to stay informed about the latest developments in welding technology and best practices. Regular training sessions and workshops can facilitate this knowledge transfer, enabling workers to adapt to new tools and techniques effectively.
The Benefits of Modern Welding Techniques
Numerous benefits accompany the adoption of advanced welding methods. These include reduced material costs, lower labor costs, improved product quality, and shorter lead times. The enhanced strength and durability of welds contribute to the longevity of the final products, reducing the need for repairs or replacements. Many manufacturers are turning to advanced welding methods as part of their commitment to sustainability. More efficient processes lead to less energy usage and reduced emissions, aligning production practices with modern environmental standards. As industries strive for efficiency, the benefits of advanced welding techniques become clearer. Investment in such methods supports immediate productivity and positions companies for future growth in an increasingly competitive market.
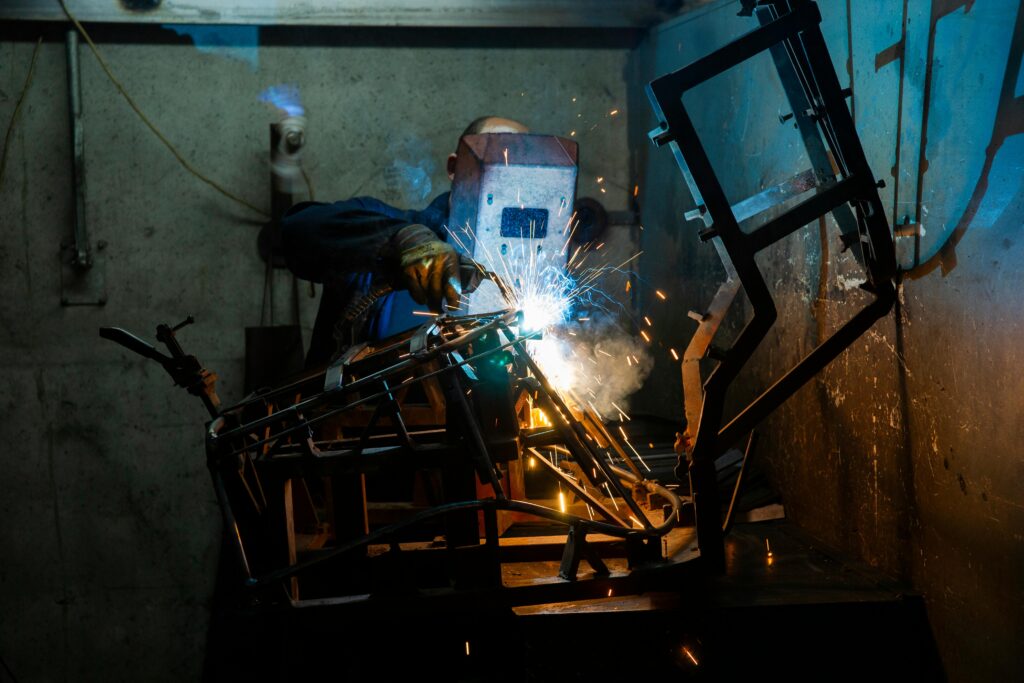
Challenges of Advanced Welding Techniques
Despite the clear advantages, the transition to advanced welding methods is not without challenges. One of the most pressing issues is the high initial investment in advanced equipment and training. Smaller companies, in particular, may struggle to afford the upfront costs associated with implementing these new technologies. The rapid evolution of welding technology means that workers must continuously update their skills. Keeping pace with these developments can be a daunting task for some businesses, especially if they lack the resources for ongoing training. This potential for skill gaps could hinder the successful adoption of advanced welding practices. Collaboration with equipment manufacturers and training organizations can help mitigate these issues. Such partnerships can provide essential insights into effective methods and offer resources for employee training, which will ultimately benefit the industry as a whole.
The Future of Welding Technology
Looking ahead, the future of welding technology appears to be bright, driven by innovations in materials and techniques. As industries push toward greater automation and smart manufacturing, welding will undoubtedly evolve as well. The integration of artificial intelligence in welding processes is being explored, with the potential to enhance precision and adaptability significantly. Research into new materials such as high-strength alloys and composites promises to create new opportunities for advanced welding applications. These developments will not only support the manufacturing of lighter and stronger products but will also enable industries to meet stringent performance requirements. As professionals within the manufacturing domain continue to embrace advanced welding technologies, the overall efficiency and productivity of industrial production will improve significantly, paving the way for new opportunities and innovations.
The impact of advanced welding methods on industrial production efficiency cannot be overstated. As manufacturers adopt these technologies, they are positioning themselves for growth in an increasingly competitive marketplace. By acknowledging the benefits, challenges, and real-world applications of these techniques, industries can harness their full potential. Investing in advanced welding methods is a strategic move to optimize production processes and a commitment to quality and sustainability in the evolving landscape of manufacturing.